Rotor blade for innovative tidal generator
At flw speeds of up to 5 m/s, the rotors of tidal generator
are subjected to high dynamic loads. In response, an
intelligent, heavy-duty CFC rotor blade has been developed and
produced by Avantgarde Technologie GmbH for the SCHOTTEL Group
using VAP® technology and process engineering
support from Composyst GmbH.
To limit the shearing forces that can occur at overspeed, the
intelligent blade adjusts in shape to enlarge its pitch angle.
This significantly reduces thrust augmentation and keeps the
load exerted on the tur bine and the supporting structure at a
low level. The high load capacity and thus operational safety
of the weight-reduced rotor blades is achieved in an integral
production concept realized in the VAP® process for
highly reliable infusion results.
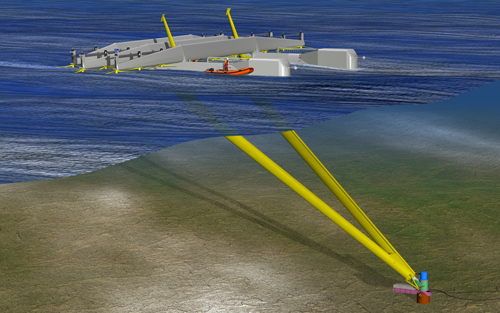 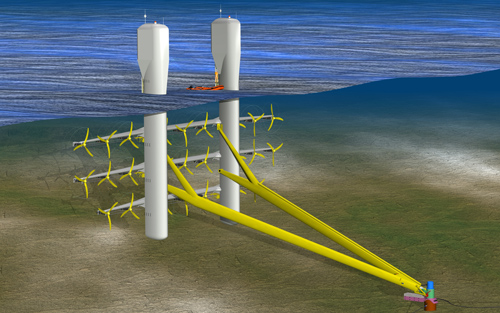
In fact, VAP® delivers mechanical design
implementation in aviation quality. The CFC preforms are
dry-stacked and can be optimally draped even in the extreme
geometry areas of the blade. By using a VAP®
membrane system by Trans-Textil GmbH, Avantgarde Technologie
also achieves homogeneous fiber volume content in the blade.
Accordingly the blade offers reliable structural properties
from its innovative load transfer hub to its tip.
|